ATTC2000 | Transfer Shuttle Conveyor
High performance for SMT lines with up to 40 programmable board models.
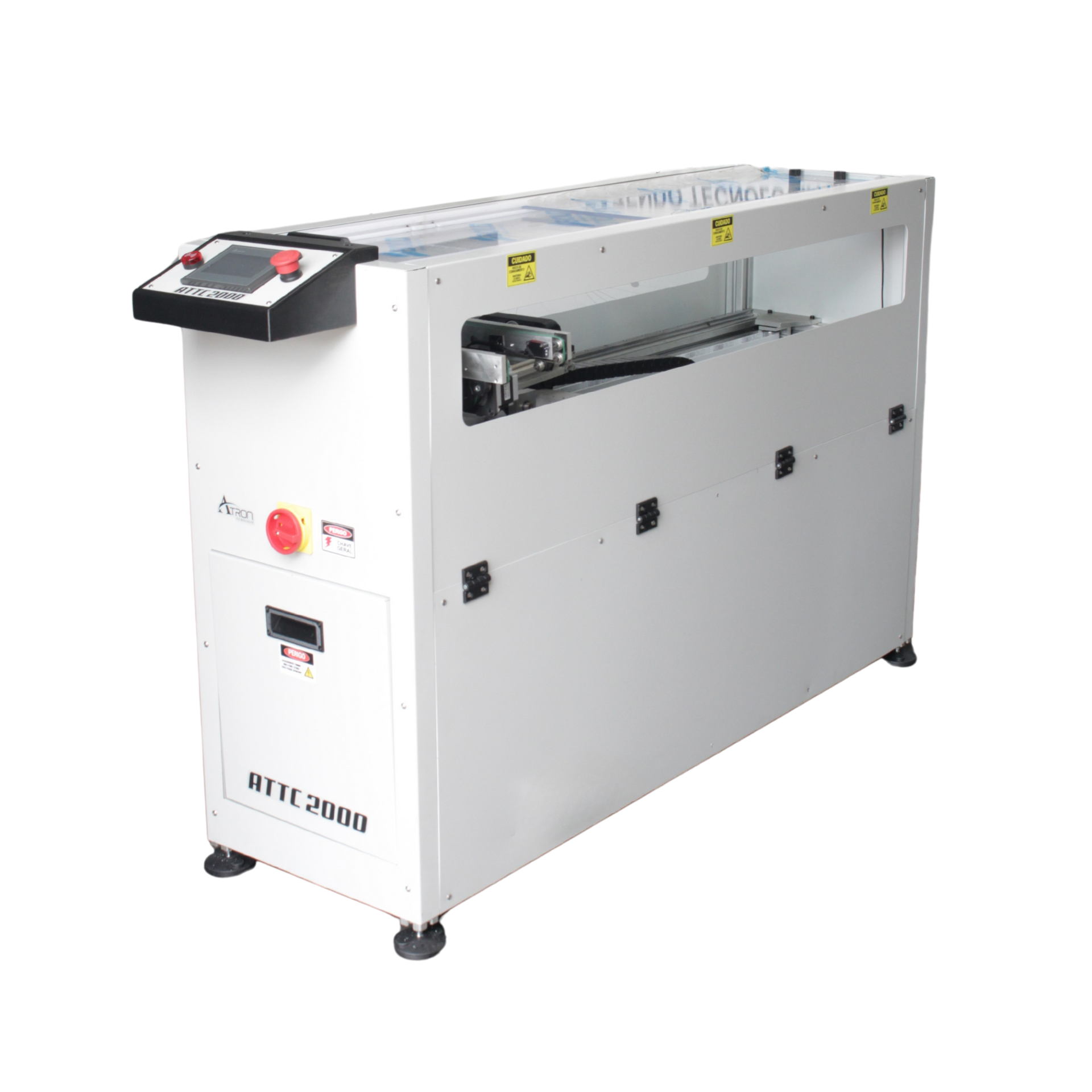
SHUTTLE CONVEYOR
The ATTC2000 is an automatic conveyor designed to transfer PCB boards between SMT equipment, even with alignment differences between conveyors. With an intuitive and easy-to-configure interface, it offers an optimized layout in national language and memory for up to 40 board models, ideal for medium and high production environments. It is the ideal solution to increase efficiency and standardization in SMT lines.
Specification
- Model: ATTC2000
- Dimensions: 2000mm x 600mm x 1200mm
- Voltage: 220V / 60Hz
- Weight: 75 kg (approx.)•Stroke: 1400 mm
- Max. PCB Width: 400 mm
- Interface: HMI with PLC
- Communication: SMEMA
________________________________________
Applications and Indications
- Ideal for medium and high SMT production;
- Compatible with different conveyors;
- Optimizes space and flow in automated lines
- High performance and operational safety
- National production with support and warranty
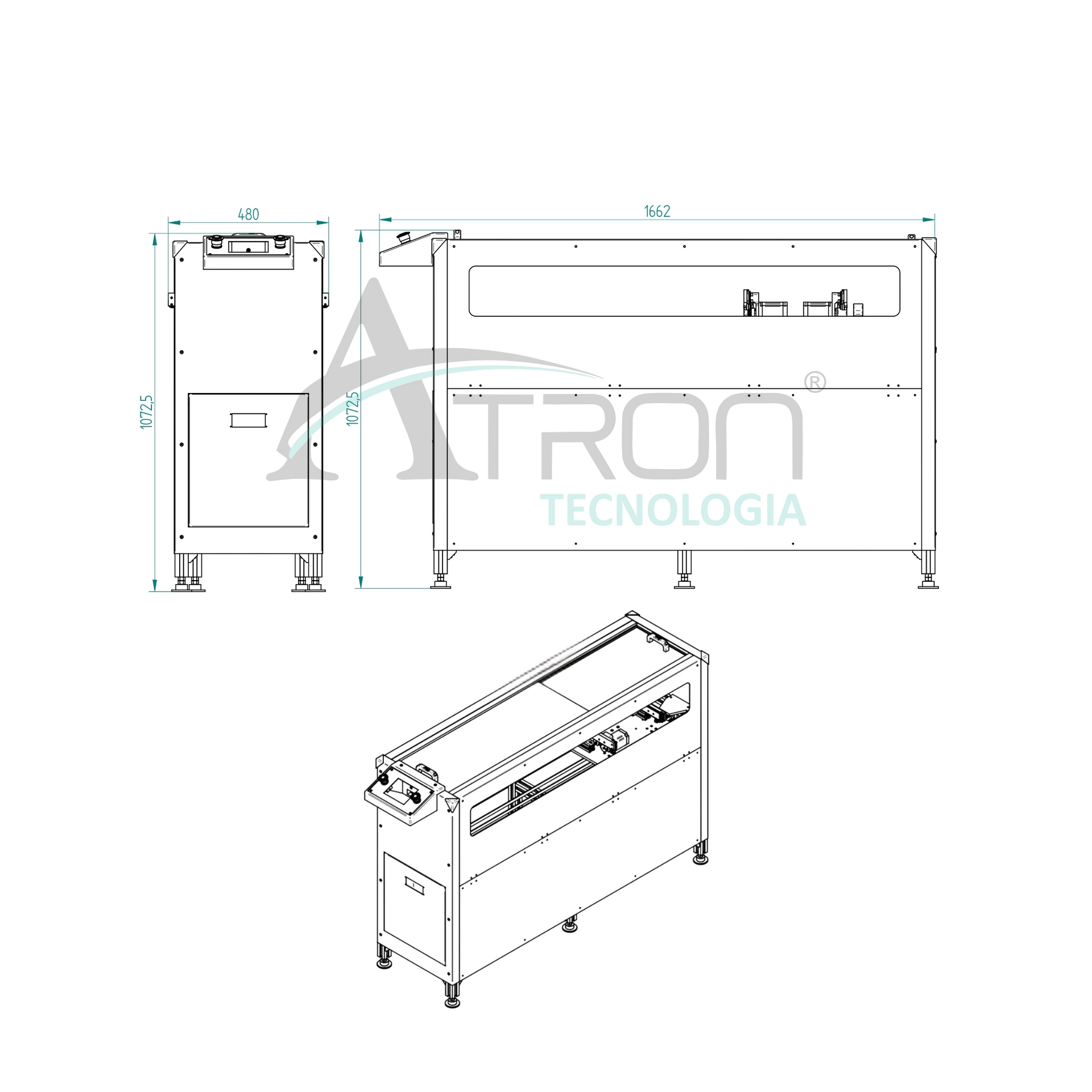
Technical description
Structure
- 40x40 aluminum profile;
- ACM and galvanized steel fairing;
- Acrylic ESD cover with handles;
Transport System
- 6mm timing belt;
- NEMA 17 stepper motors;
- 3 programmable positions via HMI;
Safety
- Closed door sensor;
- Emergency pushbutton;
- Cover with transparent viewing;
Interface and Control
- HMI inclined at 45°;
- Storage of up to 40 board models;
- Simple to configure;
Guarantee
A) Equipment:
Full manufacturer's warranty for a period of 12 (twelve) months after the date of shipment.
Shipping and returning parts under warranty to the manufacturer are the customer's responsibility.
Defects caused by improper use are excluded from the warranty.
Full parts supply warranty for 10 (ten) years.
B) Labor:
12 (twelve) months after the date of shipment.
Defects caused by improper use are excluded from the warranty.
For equipment installed outside the city of Manaus, travel and accommodation expenses for ATRON's technical personnel, incurred during equipment installation, training sessions, and technical assistance calls, will be the customer's responsibility.
Service Limitations:
Technical assistance within the service warranty period will be free of charge during business hours — MON to FRI, from 8:00 a.m. to 5:00 p.m.
Service requested outside of business hours will be charged per actual working hour, regardless of the call condition.
Coverage:
All parts and components subject to natural wear and tear, or caused by failure or lack of preventive maintenance and conservation, or by operational errors, or by intervention from unauthorized or unqualified third parties, are considered "out of warranty".
The group of wear-and-tear parts includes all movement, friction, and constantly driven units under the direct influence of external supply sources, such as compressed air, vacuum, and water. The most common include: chains, guides, pulleys, sprockets, belts, bearings, bushings, air filters, general filters, lenses, nozzles, limit switches, ejector valves, solenoid valves, pneumatic pistons, among other parts proven to be subject to movement and wear.
For services involving this group, technical hours employed in repair or replacement will be charged separately according to the standard technical hour rate in effect at the time.
Installation:
Installation will be carried out by an ATRON technician at no additional cost to the customer. However, for equipment installed outside the city of Manaus, travel, food, and accommodation expenses will be the customer’s responsibility.